EZC Sustainable Professional Services
One-stop solution
EZC conducts a comprehensive diagnosis of the printing machine before installation and provides a detailed specialist inspection report.
Upon the installation of EZC hardware, the on-site engineer will perform printing tests on the ink, paper, plate, blanket, and dampening system currently in use by the customer. These tests will be conducted based on the ISO 12647-2 offset printing standard or the G7 neutral printing density curve. This process will establish TVI curves for various commonly used papers, thereby standardizing the printing process.

01
Standardized Proofing
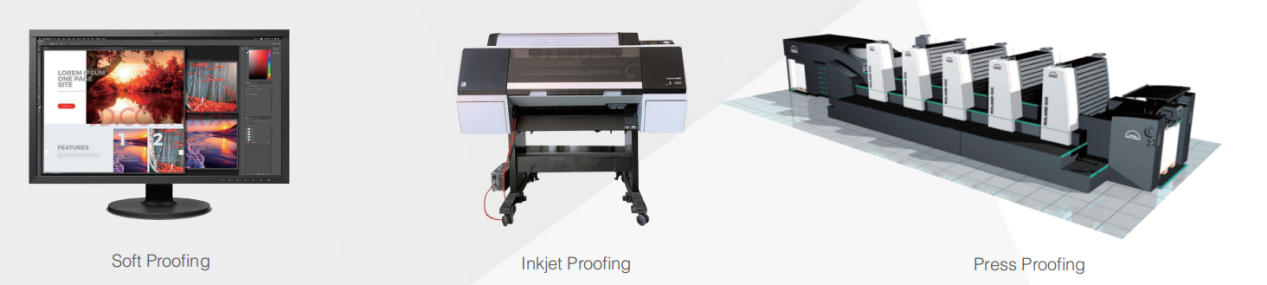
Soft Proofing
After screen soft proofing, designers can preview and control the printing effects in advance through the screen display. They can design the desired colors based on the screen display. Print operators and color matching personnel can use the screen display as a reference for printing.
Inkjet Proofing
Through digital proofing calibration, the following effects can be achieved:
1:remote proof viewing
Digital proof samples can be sent to clients by mail as a basis for approval. This allows clients to confirm the printing based on what they see in the samples, saving them the time and effort of traveling to review physical samples.
2: signing the sample in person
When customers visit the printing facility to discuss business matters and bring their files, digital proof samples can be created to provide them with an advance preview of the printing results. This allows them to directly approve the samples and sign off on the printing. During the subsequent production process, the machine operator can refer to the digital proof samples as a guide for the printing process.
3: Design Standardization
By digitally proofing the customer's source files, if the proofing is different from the customer's sample, the source file can be modified and proofed again. Repeat the above steps until the digital proof matches the customer's physical sample. Once the modified source files are approved, they can be sent for printing, and the color will be the same with proof sample when the job is run on the press, saving time on press-side color adjustments.
Press Proofing
For large volume orders, customers may need to confirm the printing results in advance. In such cases, the installed EZC system can be used for printing proofs. With EZC's one-click printing feature, the proofs can be produced directly to the standard. Once the customer approves the samples and signs off on them, the printing data is saved. When it comes to printing the actual production run, the saved printing data can be retrieved and used for one-click printing, ensuring that the printing results are consistent with the approved samples.
02
Classic Services
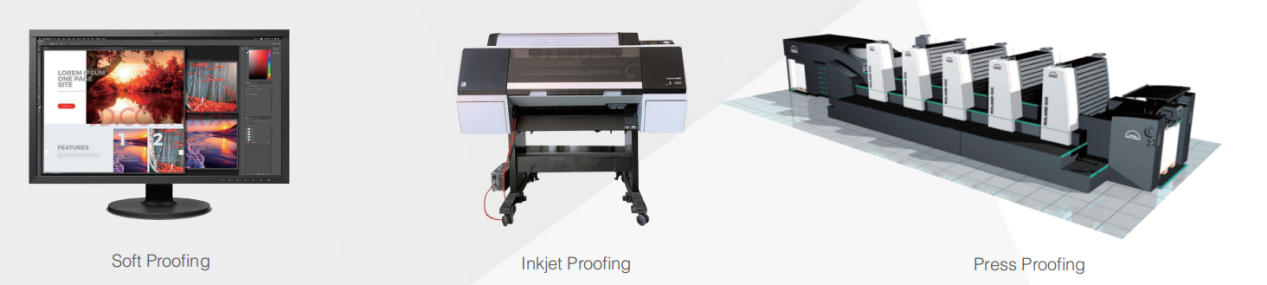
1. EZC 'Full System Check-up' (assessment of overall and individual component performance).
2. Five-year warranty on core ink pump components.
3. Expert database calibration (twice a year, including designated ink, paper, printing plates, blankets, and fountain solution).
4. Ink release curve calibration (twice a year).
5. Annual standard maintenance (twice a year).
03
Advanced Value-Added Services
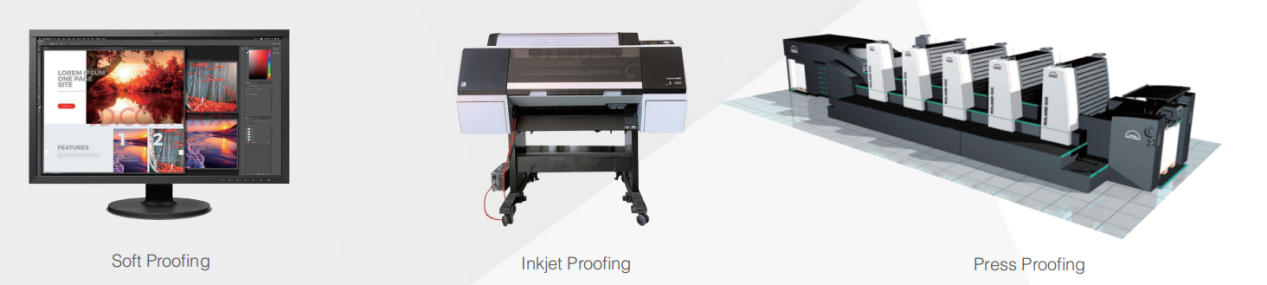
1.Expert Database Calibration Service
2.Standardized Color Management Services for Printing Company
3.Press Status Adjustment
4.Rubber Roller Status Check
04
Cloud Expert Database Service
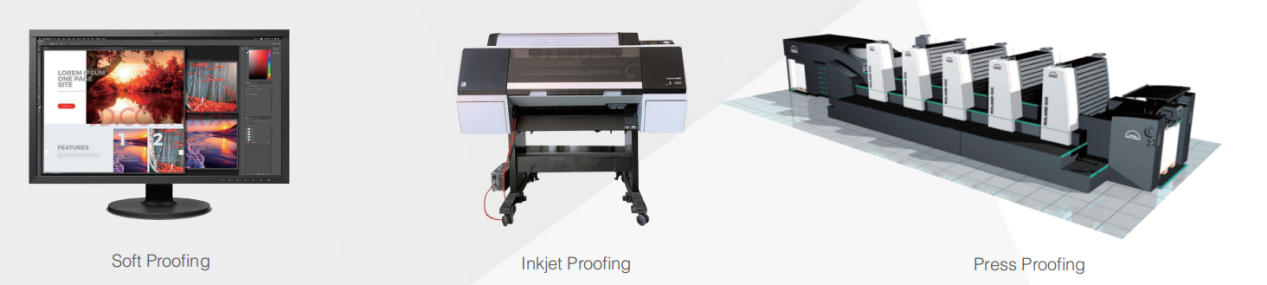
EZC offers cloud-based real-time correction and updating services for expert databases, ensuring long-term color consistency in printing.
Additionally, we provide open cloud-based online technical support services, enabling remote monitoring of equipment faults and remote services to ensure timely optimization of equipment operation.
05
Service Platform
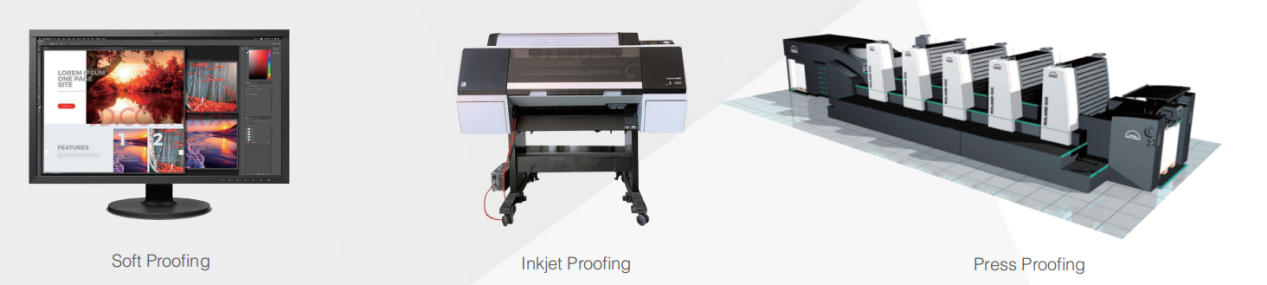
Establishing a service platform aims to address the challenges faced by printing enterprises regarding equipment services:
Lack of avenues: Sudden machine breakdowns make it difficult to find repair technicians.
Lack of assurance: The quality of repair processes cannot be guaranteed.
Lack of standards: High repair costs and poor timeliness.
Lack of trust: Substandard parts affect production due to mistrust.
Lack of oversight: Non-transparent parts pricing leads to exploitation.
Platform Positioning:
1. Establishing O2O chain service stations with standard service, rapid response, and transparent processes to enhance customer satisfaction and promote sales.
2. Innovating management models to reduce costs and improve efficiency, while integrating printing technology services for sustainable profitability, benefiting customers, distributors, manufacturers, and employees.
Our service platform's aim: Prompt responsiveness, professional standards, authentic parts, fairness, reliability, and transparent processes.